В этом году легендарная марка MINI вернулась в автоспорт. Компания Prodrive подготовила специализированную раллийную версию автомобиля для участия в FIA World Rally Championship, главном мировом чемпионате. В ходе подготовки машин Prodrive активно использовала все самые современные технологии проектирования и изготовления компонент, в том числе и средства 3D печати, причем не только для создания прототипов, но и для изготовления реальных «боевых» деталей, штатно устанавливаемых на гоночные автомобили.
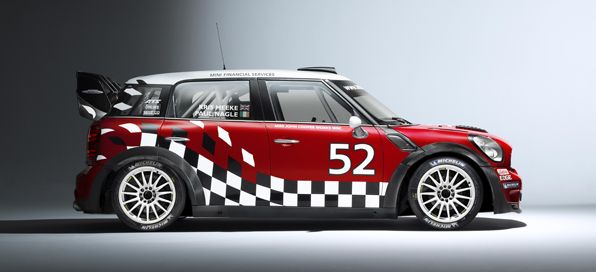
Видя успешное развитие MINI, концерн BMW усилил сотрудничество с Prodrive, чтобы включить MINI WRC для официального участия в World Rally Championship в 2011 году. «Мы все очень хотели стать заводской командой потому, что это повышает значимость и узнаваемость проекта» говорит Пол До (Paul Doe) ведущий инженер проекта MINI WRC в Prodrive. Объем работ, который необходимо выполнить для каждой из восьми заводских и 20-ти клиентских машин, просто невероятен, это составляет сотни часов для одного кузова. Чтобы ускорить этот процесс в Prodrive для изготовления некоторых деталей прибегли к Direct Digital Manufacturing (DDM) с использованием технологии FDM (англ. Fused Deposition Modeling , Моделирование методом наплавления). После некоторого тестирования было выяснено, что такие детали достаточно прочны для установки непосредственно на автомобиль.
Для восьми машин заводской команды воздуховоды, воздухозаборники и обтекатели тормозов изготавливаются на принтере Dimension, тем самым экономится время и расходы на дорогостоящую оснастку и литье. Для Доу и остальной команды это оказалось быстрым решением, которое оказалось и достаточно надежным, чтобы работать по-настоящему.
«Иногда это было что-то срочно нужное, но вряд ли изготавливаемое другим способом, так что мы бы делали модель в САПР и оперативно отправляли на печать, в некоторых случаях деталь была готова буквально через пару часов и она устанавливалась в ту же ночь» объясняет Доу.
«Вы можете создать дизайн, совершенно «неизготовляемый» обычными методами, или, как минимум неизготовляемый адекватным способом. Вместо изготовления пяти углепластиковых секций, затем их соединения, сложного крепления, мы просто проектируем единственную деталь и отправляем ее на печать и все это работает!»
В большинстве своем, части, изготавливаемые на 3D принтере, не предполагают несения существенных нагрузок. В автомобиле достаточно много прочных частей, но в то же время есть множество элементов, не испытывающих серьезных нагрузок, но требующих изготовления тем или иным способом.
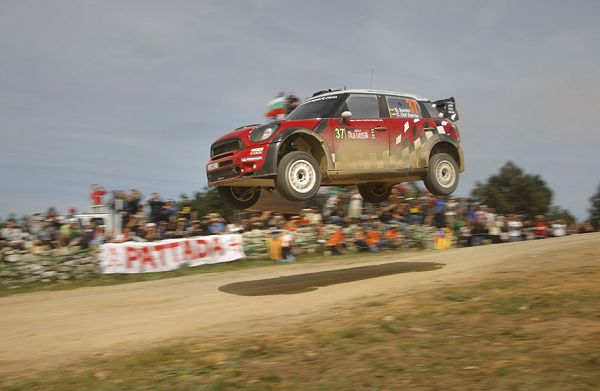
«Долгое время мы непростительно не пользовались 3D принтером, что теперь кажется странным» говорит Доу. «Сейчас мы почти достигли предела загруженности машины – очень нечасто ее можно увидеть простаивающей, даже если мы уже прошли фазу прототипирования. Принтер теперь загружен даже больше, чем это было на этапе разработки». Это все следствие того, что на автомобиль теперь устанавливаются детали, полностью изготовленные на 3D принтере.
Некоторые детали MINI WRC, изготавливаемые методом 3D печати:
- Воздушный фильтр. Нижний «раструб» для огромного воздушного фильтра исходно был изготовлен в качестве макета для физической проверки конструкторских решений. «Затем мы изготовили модель с чуть большей толщиной стенок, т.к. не были уверены в надежности материала. Эта модель прошла два цикла испытаний и никогда нас не подвела, не сломалась, мы были удивлены и оставили деталь в качестве штатной» - комментирует Пол Доу.
- Оконный воздуховод. По сути – это воздушный фильтр для системы вентиляции салона. Его лабиринт перекрывает доступ дождевым каплям, пыли и другому мусору от проникновения в кабину. Его сложная форма требовала бы изготовления и сборки из пяти углепластиковых частей, сложной и дорогостоящей оснастки. Изготовление на 3D принтере зацело значительно сэкономило время и расходы.
- Расширитель задней арки колес. Руководящим спортивным органом не понравилась исходная конструкция задних арок MINI – она оказалась чересчур открытой. В результате грозил запрет на допуск к соревнованиям. Расширяющие лепестки нужной формы были изготовлены и установлены на место за ночь, таким образом, на второй день экспертизы инспектора FIA дали «добро».
- Воздухозаборник на капоте. За несколько часов до официального представления автомобиля двигателисты BMW потребовали доработки – дополнительного воздухозаборника на капоте. Нужная деталь была напечатана буквально в последние минуты перед презентацией. Позже она была доработана для увеличения прочности.
- Кронштейн экрана компьютера. Кронштейн настраивается по высоте индивидуально для каждого водителя. Гонщики предпочитают его положение таким, чтобы иметь лучший обзор, в то время как инженеры предпочитают расположить его как можно ниже – 3D печать помогла найти идеальное компромиссное решение.
- Спидометр / тахометр. Этот элемент специально разработан для изготовления на 3D принтере. Он включает в себя большой ЖК-дисплей для отображения передач /оборотов и скрывает внутренние компоненты проводки.
www.prodrive.com